Descripción general del proyecto
1. Programa de producción
600 juegos/día (pedestal de rodamiento 117/118)
2. Requisitos para la línea de procesamiento:
1) Centro de mecanizado NC adecuado para línea de producción automática;
2) Abrazadera hidráulica para vestido;
3) Dispositivo automático de carga y corte y dispositivo de transporte;
4) Tecnología de procesamiento general y tiempo del ciclo de procesamiento;
Disposición de las líneas de producción
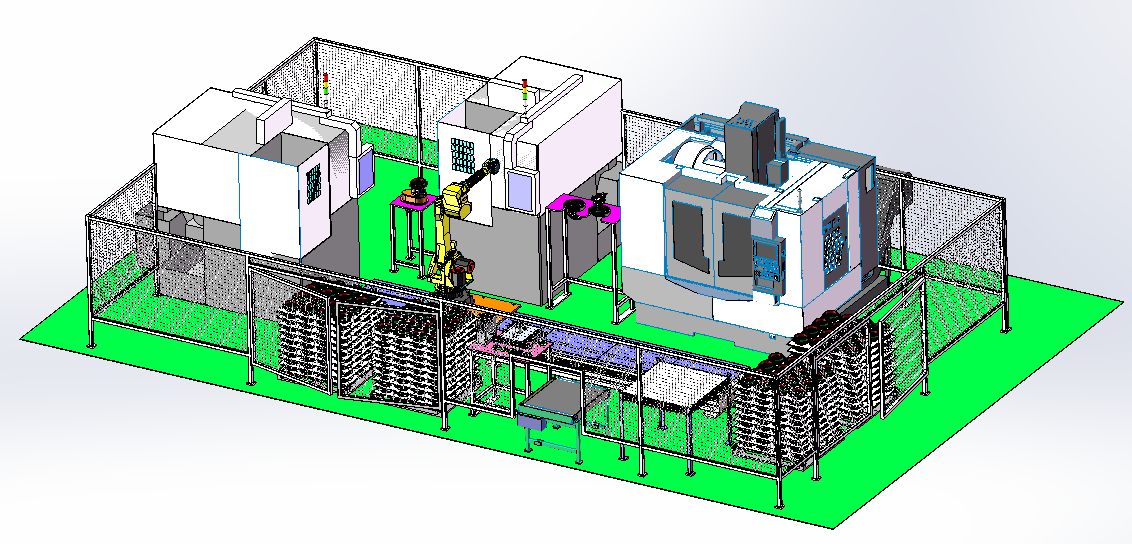
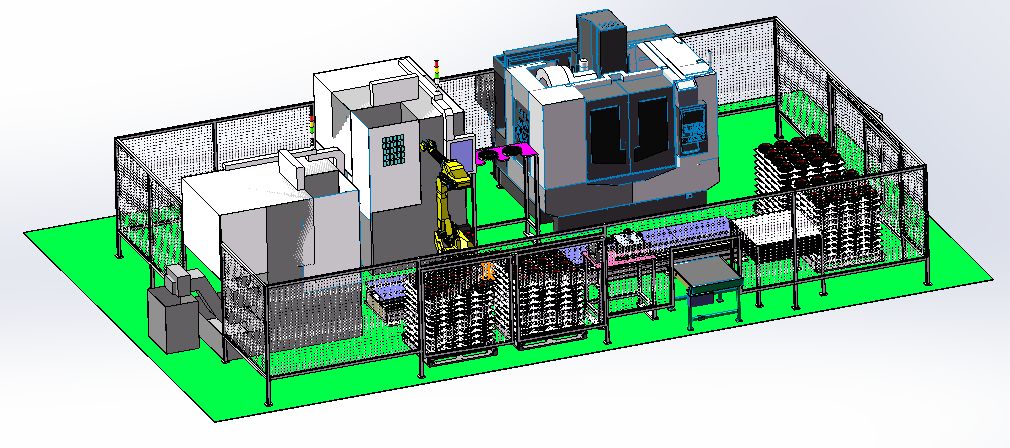
Disposición de las líneas de producción
Introducción de acciones del robot:
1. Coloque manualmente las cestas mecanizadas y colocadas de forma aproximada en la mesa de carga (Mesas de carga N° 1 y N° 2) y presione el botón para confirmar;
2. El robot se mueve a la bandeja de la mesa de carga No. 1, abre el sistema de visión, agarra y mueve las Partes A y B respectivamente a la estación de visualización angular para esperar la instrucción de carga;
3. La estación de reconocimiento angular envía la instrucción de carga. El robot coloca la pieza n.° 1 en el área de posicionamiento de la plataforma giratoria. Gira la plataforma giratoria e inicia el sistema de reconocimiento angular, determina la posición angular, detiene la plataforma giratoria y finaliza el reconocimiento angular de la pieza n.° 1.
4. El sistema de reconocimiento angular envía la orden de supresión, y el robot recoge la pieza n.° 1 y coloca la n.° 2 para su identificación. La plataforma giratoria gira y el sistema de reconocimiento angular se activa para determinar la posición angular. La plataforma giratoria se detiene, se completa el reconocimiento angular de la pieza n.° 2 y se envía la orden de supresión.
5. El robot recibe la orden de corte del torno vertical n.° 1 y se desplaza a la posición de carga y corte del torno vertical n.° 1 para cortar y cargar el material. Una vez finalizada la acción, comienza el ciclo de mecanizado de una sola pieza del torno vertical.
6. El robot toma los productos terminados del torno vertical N°1 y los coloca en la posición N°1 de la mesa de volteo de piezas de trabajo;
7. El robot recibe el comando de corte del torno vertical n.º 2, se mueve a la posición de carga y corte del torno vertical n.º 2 para cortar y cargar el material, y luego se completa la acción y comienza el ciclo de procesamiento de una sola pieza del torno vertical;
8. El robot toma los productos terminados del torno vertical n.º 2 y los coloca en la posición n.º 2 de la mesa de volteo de piezas de trabajo;
9. El robot espera el comando de corte del mecanizado vertical;
10. El mecanizado vertical envía la orden de corte, y el robot se desplaza a las posiciones de carga y corte del mecanizado vertical, agarra y desplaza las piezas de las estaciones n.° 1 y n.° 2, respectivamente, a la bandeja de corte, y las coloca en la bandeja. El robot se desplaza a la mesa de volteo para agarrar y enviar las piezas n.° 1 y n.° 2 a las posiciones de carga y corte del mecanizado vertical, respectivamente, y las coloca en el área de posicionamiento de las estaciones n.° 1 y n.° 2 de la pinza hidráulica, respectivamente, para completar la carga del mecanizado vertical. El robot sale de la distancia de seguridad del mecanizado vertical e inicia un ciclo de procesamiento.
11. El robot se desplaza a la bandeja de carga nº 1 y se prepara para el inicio del programa del ciclo secundario;
Descripción:
1. El robot coloca 16 piezas (una capa) en la bandeja de carga. Reemplaza la pinza de succión y coloca la placa divisoria en la cesta de almacenamiento temporal.
2. El robot empaca 16 piezas (una capa) en la bandeja de almacenamiento. El robot debe reemplazar la pinza de la ventosa una vez y colocar la placa divisoria sobre la superficie divisoria de las piezas de la cesta de almacenamiento temporal.
3. De acuerdo con la frecuencia de inspección, asegúrese de que el robot coloque una pieza en la mesa de muestreo manual;
1 | El cronograma del ciclo de mecanizado | ||||||||||||||
2 | Cliente | Material de la pieza de trabajo | QT450-10-GB/T1348 | Modelo de máquina herramienta | Archivo No. | ||||||||||
3 | Nombre del producto | 117 Asiento del cojinete | Dibujo No. | DZ90129320117 | Fecha de preparación | 04/01/2020 | Preparado por | ||||||||
4 | Paso del proceso | Cuchillo No. | contenido de mecanizado | Nombre de la herramienta | Diámetro de corte | Velocidad de corte | Velocidad de rotación | Avance por revolución | Alimentación por máquina herramienta | Número de esquejes | Cada proceso | Tiempo de mecanizado | Tiempo de inactividad | Tiempo de rotación de cuatro ejes | Tiempo de cambio de herramienta |
5 | No. | No. | Descripciones | Herramientas | Re mm | n | R pm | mm/Rev | mm/min | Veces | mm | Segundo | Segundo | Segundo | |
6 | ![]() | ||||||||||||||
7 | 1 | T01 | Fresado de la superficie del orificio de montaje | Diámetro de la fresa de 40 caras | 40.00 | 180 | 1433 | 1.00 | 1433 | 8 | 40.0 | 13.40 | 8 | 4 | |
8 | Taladre 17 orificios de montaje de diámetro | TALADRO COMBINADO DIA 17 | 17.00 | 100 | 1873 | 0,25 | 468 | 8 | 32.0 | 32.80 | 8 | 4 | |||
9 | T03 | Biselado posterior de orificios DIA 17 | Fresa de biselado inverso | 16.00 | 150 | 2986 | 0.30 | 896 | 8 | 30.0 | 16.08 | 16 | 4 | ||
10 | Descripción: | Tiempo de corte: | 62 | Segundo | Tiempo de sujeción con dispositivo de fijación y de carga y troquelado de materiales: | 30.00 | Segundo | ||||||||
11 | Tiempo auxiliar: | 44 | Segundo | Total de horas-hombre de mecanizado: | 136.27 | Segundo |
1 | El cronograma del ciclo de mecanizado | |||||||||||||||||
2 | Cliente | Material de la pieza de trabajo | QT450-10-GB/T1348 | Modelo de máquina herramienta | Archivo No. | |||||||||||||
3 | Nombre del producto | 118 Asiento del cojinete | Dibujo No. | DZ90129320118 | Fecha de preparación | 04/01/2020 | Preparado por | |||||||||||
4 | Paso del proceso | Cuchillo No. | contenido de mecanizado | Nombre de la herramienta | Diámetro de corte | Velocidad de corte | Velocidad de rotación | Avance por revolución | avance por máquina herramienta | Número de esquejes | Cada proceso | Tiempo de mecanizado | Tiempo de inactividad | Tiempo de rotación de cuatro ejes | Tiempo de cambio de herramienta | |||
5 | No. | No. | Descripciones | Herramientas | Re mm | n | R pm | mm/Rev | mm/min | Veces | mm | Segundo | Segundo | Segundo | ||||
6 | ![]() | |||||||||||||||||
7 | 1 | T01 | Fresado de la superficie del orificio de montaje | Diámetro de la fresa de 40 caras | 40.00 | 180 | 1433 | 1.00 | 1433 | 8 | 40.0 | 13.40 | 8 | 4 | ||||
8 | T02 | Taladre 17 orificios de montaje de diámetro | TALADRO COMBINADO DIA 17 | 17.00 | 100 | 1873 | 0,25 | 468 | 8 | 32.0 | 32.80 | 8 | 4 | |||||
9 | T03 | Biselado posterior de orificios DIA 17 | Fresa de biselado inverso | 16.00 | 150 | 2986 | 0.30 | 896 | 8 | 30.0 | 16.08 | 16 | 4 | |||||
10 | Descripción: | Tiempo de corte: | 62 | Segundo | Tiempo de sujeción con dispositivo de fijación y de carga y troquelado de materiales: | 30.00 | Segundo | |||||||||||
11 | Tiempo auxiliar: | 44 | Segundo | Total de horas-hombre de mecanizado: | 136.27 | Segundo | ||||||||||||
12 |
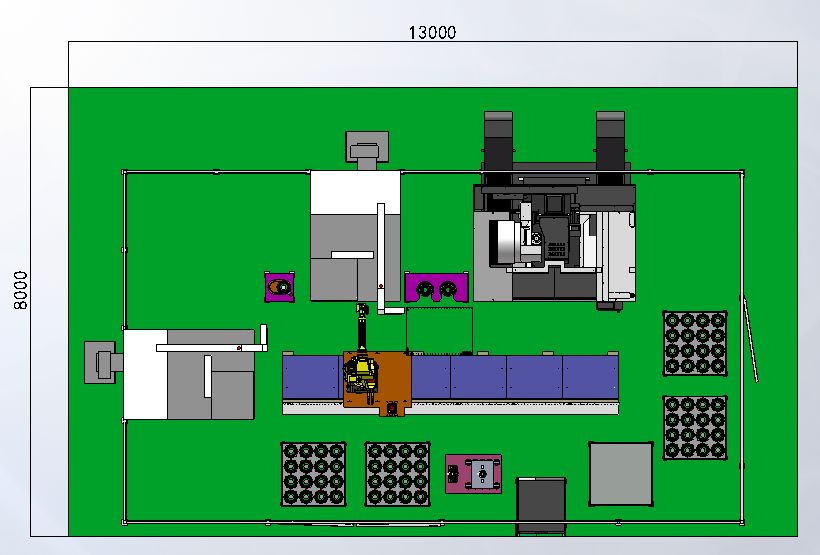
Área de cobertura de la línea de producción
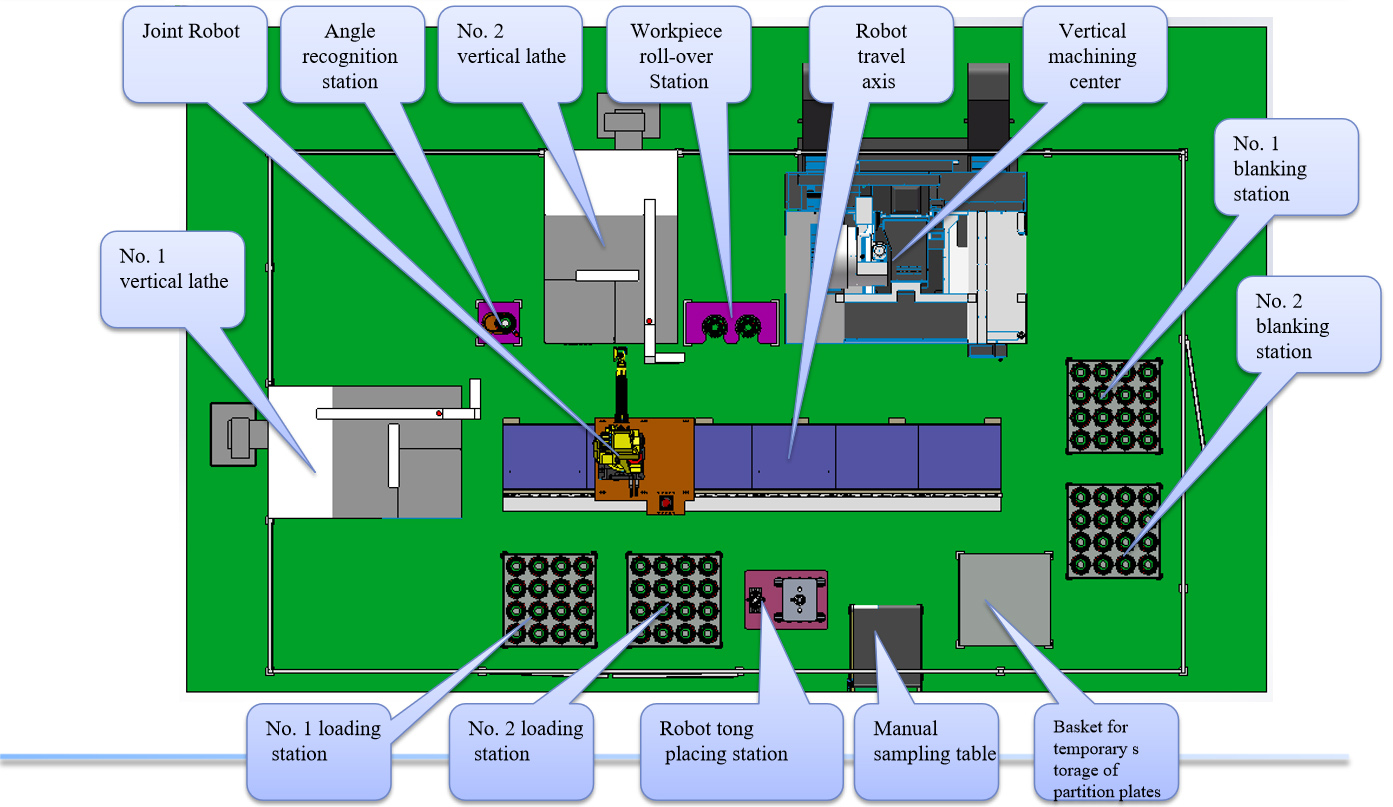
Introducción de los principales componentes funcionales de la línea de producción.
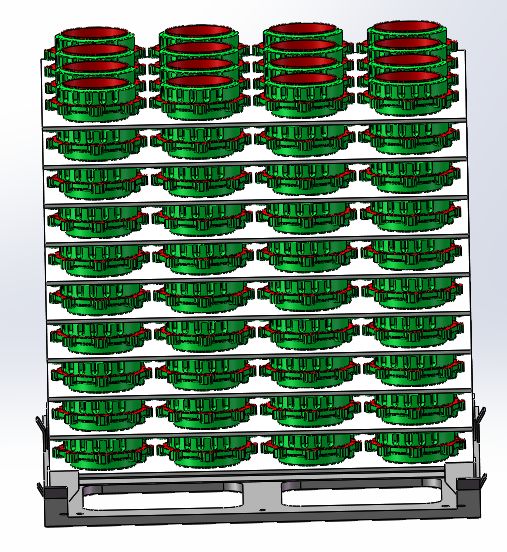
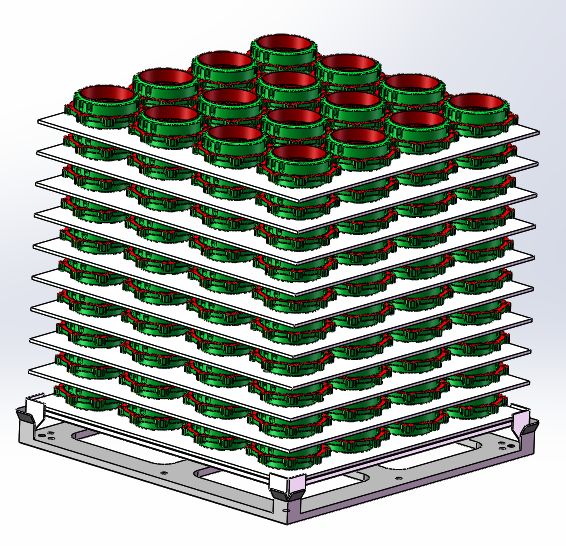
Introducción del sistema de carga y tamizado
El equipo de almacenamiento para la línea de producción automática en este esquema es: la bandeja apilada (la cantidad de piezas a empacar en cada bandeja se negociará con el cliente), y la posición de la pieza de trabajo en la bandeja se determinará después de proporcionar un dibujo 3D de la pieza de trabajo en blanco o el objeto real.
1. Los trabajadores embalan las piezas procesadas de forma aproximada en la bandeja de material (como se muestra en la figura) y las elevan con una carretilla elevadora hasta la posición designada;
2. Después de reemplazar la bandeja de la carretilla elevadora, presione manualmente el botón para confirmar;
3. El robot agarra la pieza de trabajo para realizar el trabajo de carga;
Introducción del eje de desplazamiento del robot
La estructura se compone de un robot articulado, un servomotor y un sistema de piñón y cremallera, lo que permite al robot realizar movimientos rectilíneos de ida y vuelta. Realiza la función de un solo robot que atiende múltiples máquinas herramienta y sujeta piezas en varias estaciones, lo que permite ampliar la cobertura de trabajo de los robots articulados.
La pista de viaje aplica la base soldada con tubos de acero y es impulsada por servomotor, piñón y cremallera, para aumentar la cobertura de trabajo del robot conjunto y mejorar efectivamente la tasa de utilización del robot; La pista de viaje está instalada en el suelo;
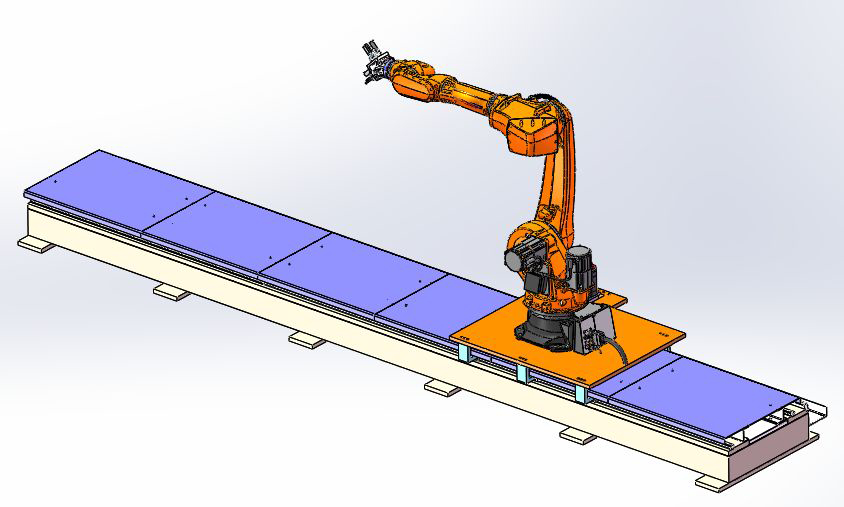
Robot Chenxuan: SDCX-RB500
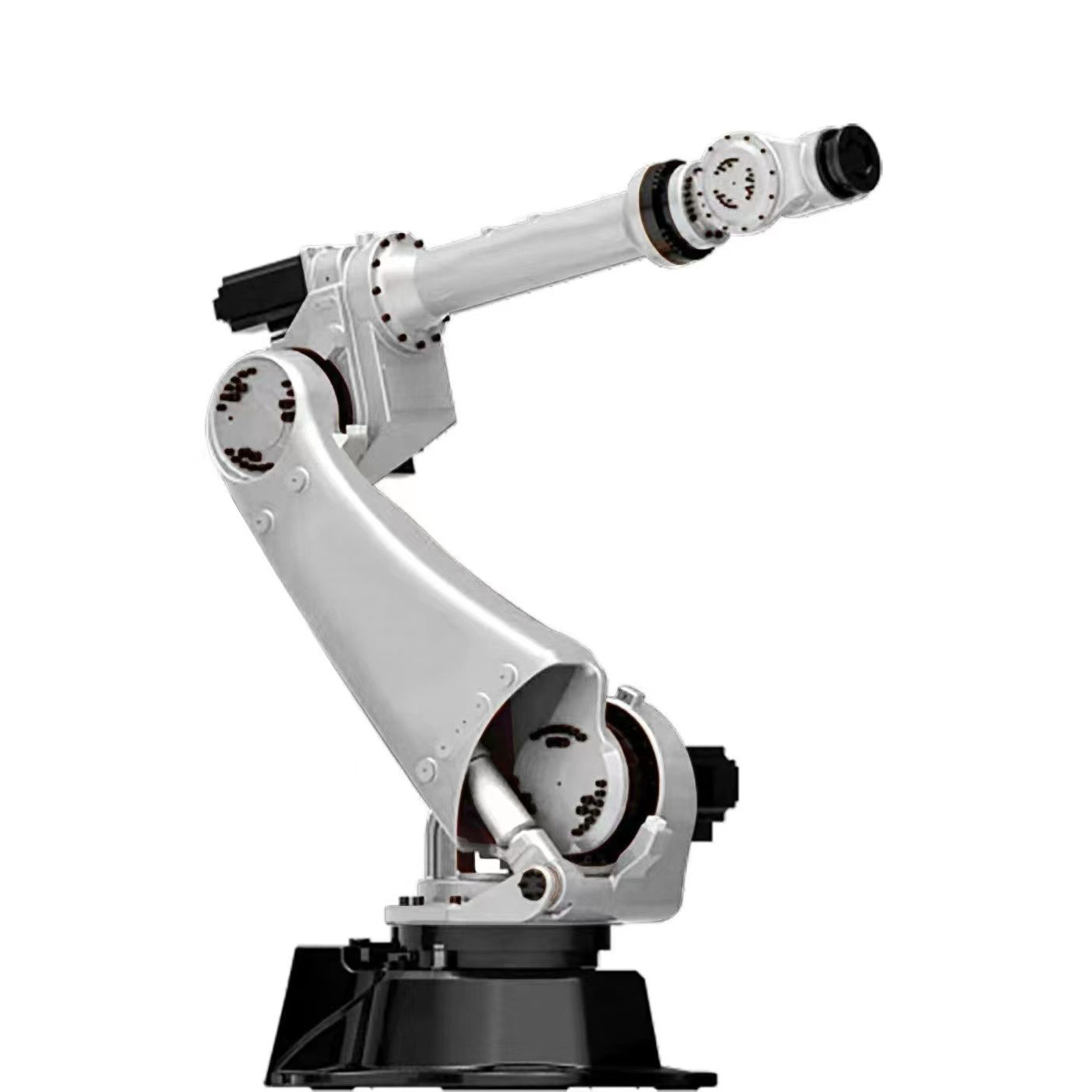
Datos básicos | |
Tipo | SDCX-RB500 |
Número de ejes | 6 |
Cobertura máxima | 2101 mm |
Repetibilidad de pose (ISO 9283) | ±0,05 mm |
Peso | 553 kilos |
Clasificación de protección del robot | Grado de protección, IP65 / IP67muñeca en línea(IEC 60529) |
Posición de montaje | Techo, ángulo de inclinación admisible ≤ 0º |
Acabado superficial, pintura. | Marco base: negro (RAL 9005) |
Temperatura ambiente | |
Operación | 283 K a 328 K (0 °C a +55 °C) |
Almacenamiento y transporte | 233 K a 333 K (-40 °C a +60 °C) |
Con un amplio rango de movimiento en la parte trasera e inferior del robot, este modelo puede montarse con elevación de techo. Gracias a la reducida anchura lateral del robot, es posible instalarlo cerca del robot, la abrazadera o la pieza de trabajo adyacente. Movimiento de alta velocidad desde la posición de espera hasta la posición de trabajo y posicionamiento rápido en desplazamientos cortos.
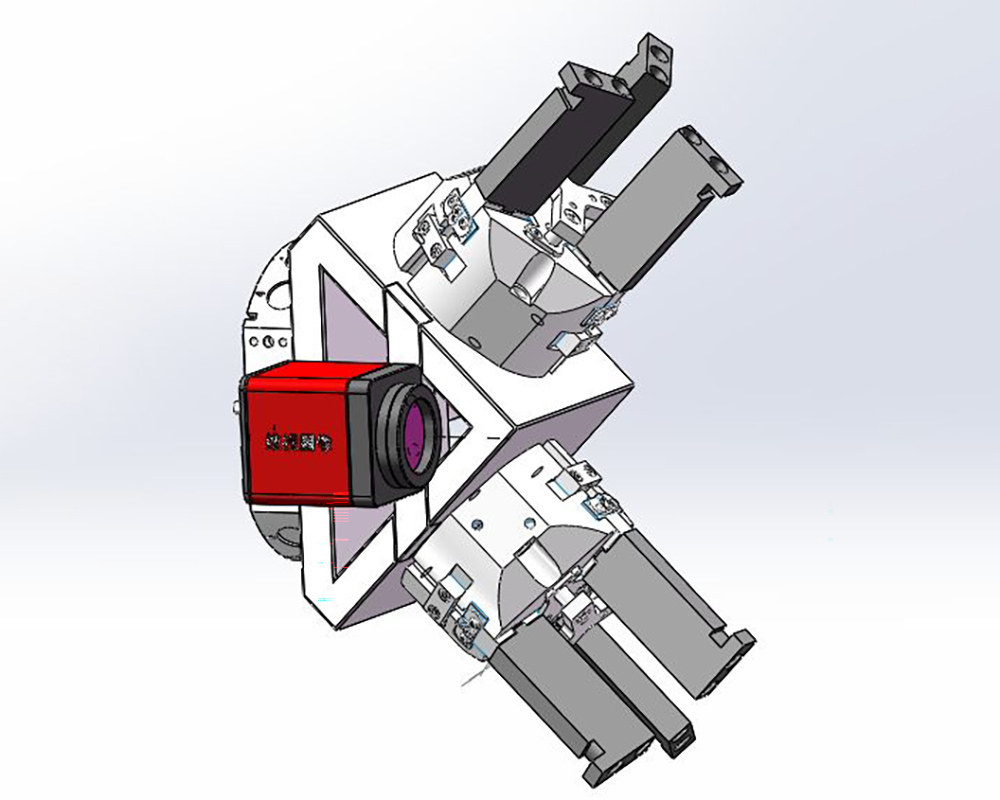
Mecanismo de pinza de carga y corte de robot inteligente
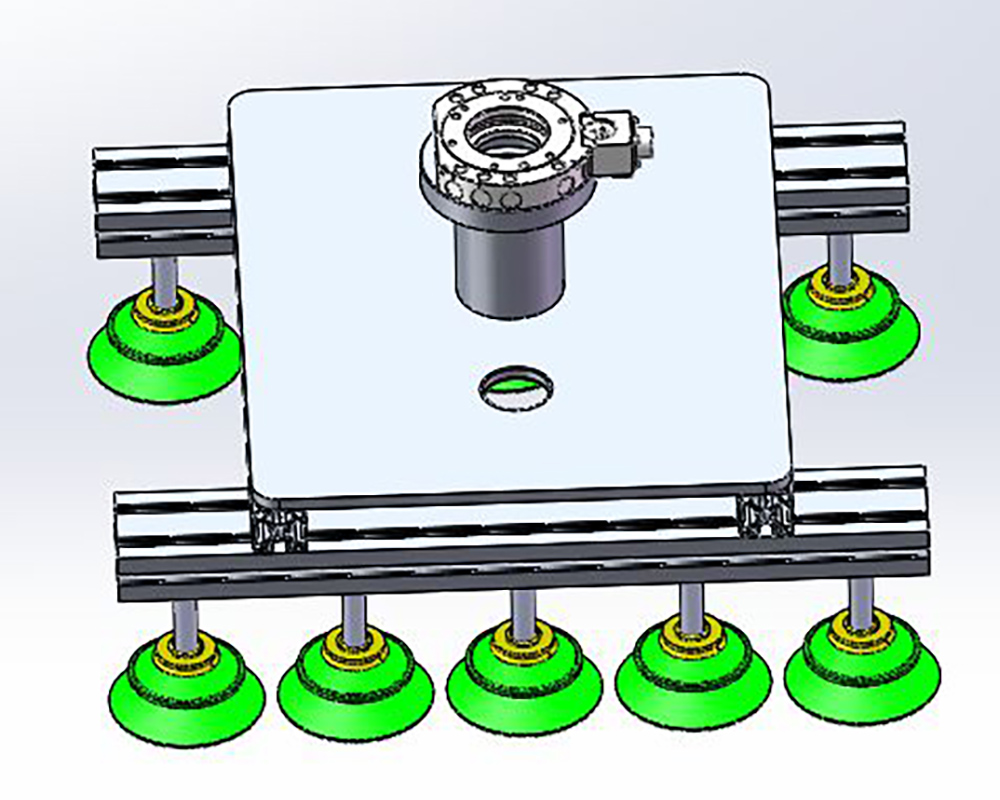
Mecanismo de pinza para placa divisoria robótica
Descripción:
1. Considerando las características de esta pieza, utilizamos el método de soporte externo de tres garras para cargar y troquelar los materiales, lo que puede lograr un giro rápido de las piezas en la máquina herramienta;
2. El mecanismo está equipado con el sensor de detección de posición y el sensor de presión para detectar si el estado de sujeción y la presión de las piezas son normales;
3. El mecanismo está equipado con un presurizador, y la pieza de trabajo no se caerá en poco tiempo en caso de corte de energía y corte de gas del circuito de aire principal;
4. Se incorpora un dispositivo de cambio de mano. El mecanismo de cambio de pinzas permite sujetar rápidamente diferentes materiales.
Introducción del dispositivo de cambio de pinzas
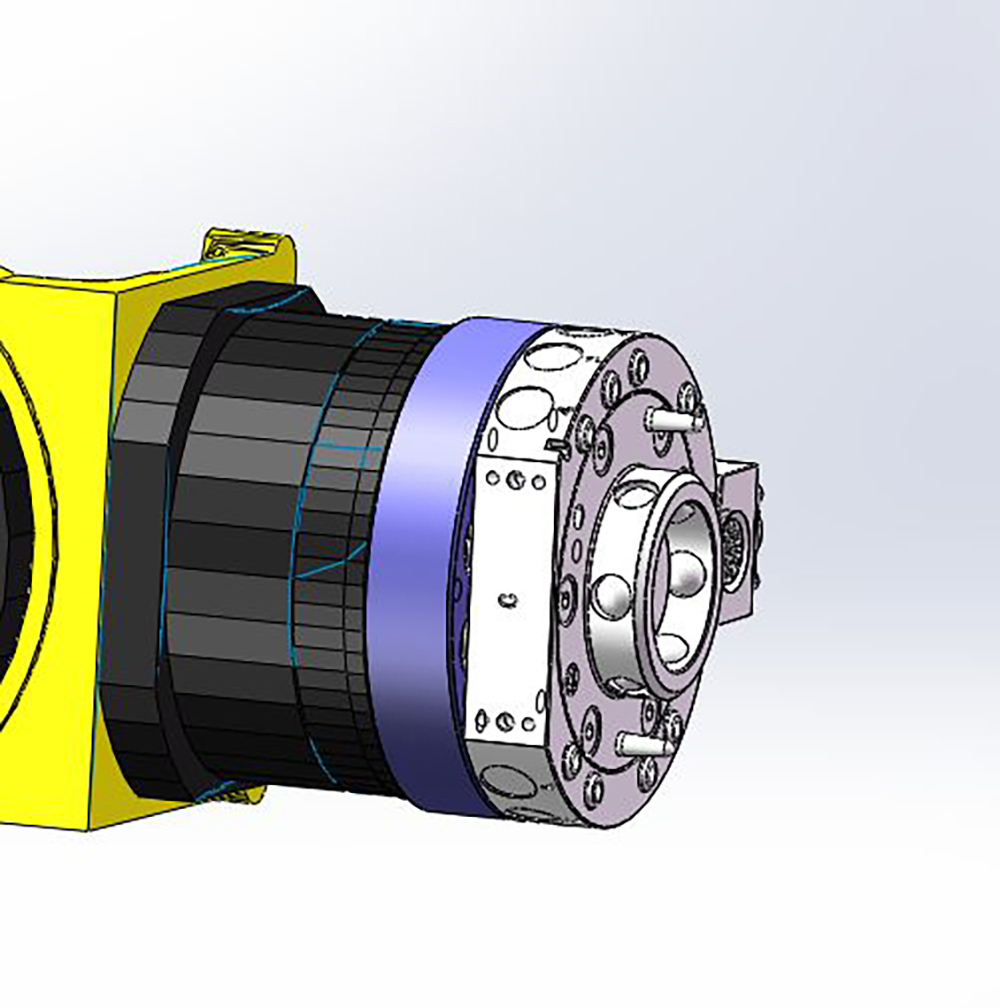
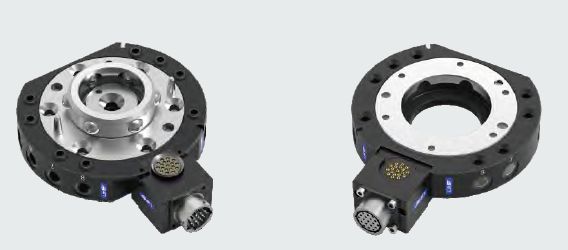
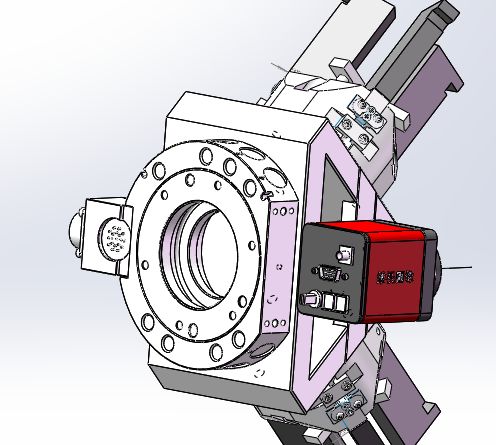
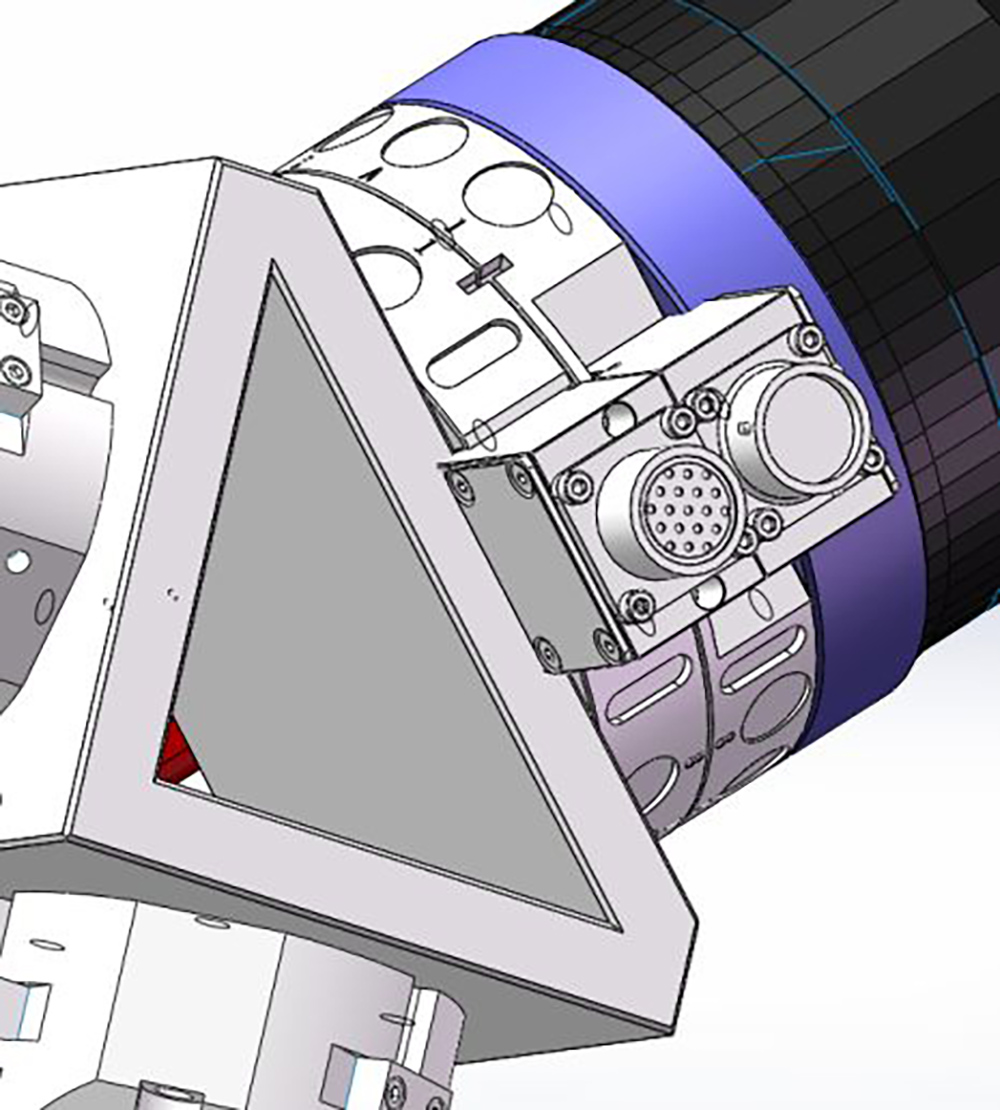
El dispositivo preciso para cambiar pinzas permite cambiar rápidamente las pinzas, los extremos de las herramientas y otros actuadores del robot. Reduce el tiempo de inactividad de la producción y aumenta la flexibilidad del robot. Se caracteriza por:
1. Desbloquee y ajuste la presión de aire;
2. Se pueden utilizar diversos módulos de potencia, líquido y gas;
3. La configuración estándar puede conectarse rápidamente con la fuente de aire;
4. Las agencias de seguros especiales pueden prevenir el riesgo de corte accidental del gas;
5. Sin fuerza de reacción del resorte; 6. Aplicable al campo de la automatización;
Introducción al sistema de visión: cámara industrial
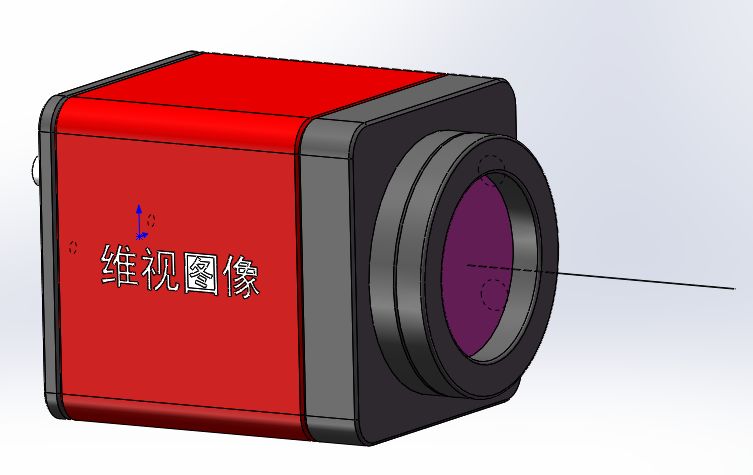
1. La cámara adopta chips CCD y CMDS de alta calidad, que tienen las características de alta relación de resolución, alta sensibilidad, alta relación señal-frecuencia, amplio rango dinámico, excelente calidad de imagen y capacidad de restauración de color de primera clase;
2. La cámara de matriz de área tiene dos modos de transmisión de datos: interfaz GIGabit Ethernet (GigE) e interfaz USB3.0;
3. La cámara tiene una estructura compacta, aspecto compacto, es ligera y está instalada. Alta velocidad de transmisión, alta capacidad antiinterferencias y una salida estable de imágenes de alta calidad. Es aplicable a la lectura de códigos, la detección de defectos, la DCR y el reconocimiento de patrones. La cámara a color tiene una excelente capacidad de restauración del color, ideal para escenarios con altos requisitos de reconocimiento de color.
Introducción del sistema de reconocimiento automático angular
Introducción a la función
1. El robot sujeta las piezas de las cestas de carga y las envía a la zona de posicionamiento del plato giratorio;
2. El plato giratorio gira bajo el accionamiento del servomotor;
3. El sistema visual (cámara industrial) funciona para identificar la posición angular y el plato giratorio se detiene para determinar la posición angular requerida;
4. El robot saca la pieza de trabajo y coloca otra pieza para la identificación angular;
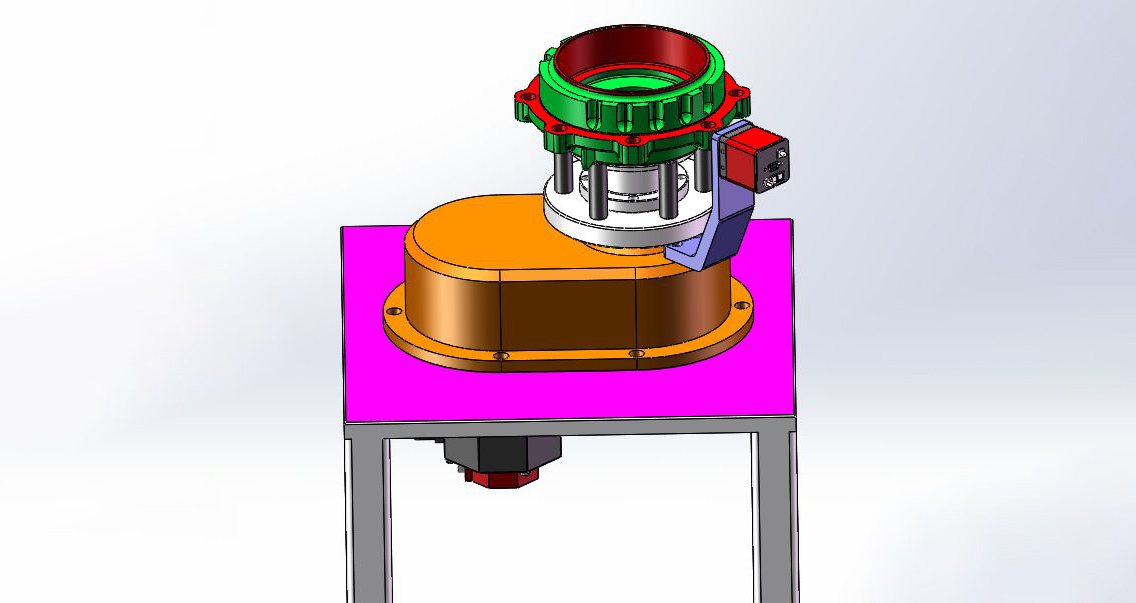
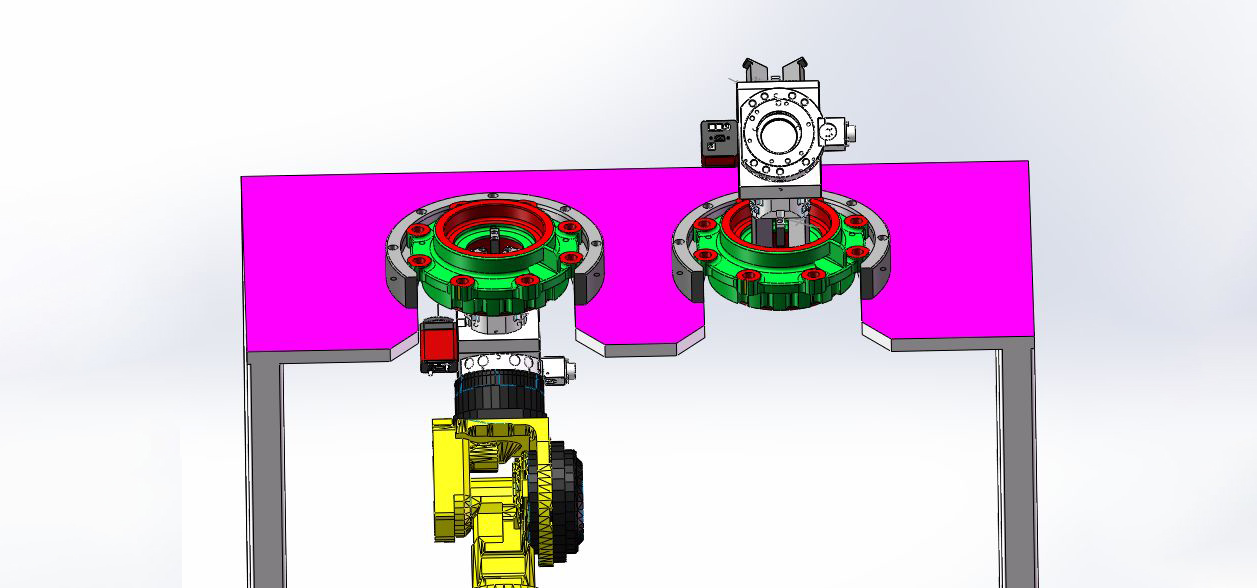
Introducción a la mesa de volteo de piezas de trabajo
Estación de vuelco:
1. El robot toma la pieza de trabajo y la coloca en el área de posicionamiento en la mesa de vuelco (la estación izquierda en la figura);
2. El robot agarra la pieza de trabajo desde arriba para realizar el giro de la pieza de trabajo;
Mesa de colocación de pinzas robóticas
Introducción a la función
1. Después de cargar cada capa de piezas, la placa divisoria en capas se colocará en la canasta de almacenamiento temporal para las placas divisorias;
2. El robot puede reemplazar rápidamente las pinzas de ventosa mediante el dispositivo de cambio de pinzas y quitar las placas divisorias;
3. Luego de que las placas divisorias estén bien colocadas, retire la pinza de ventosa y reemplácela con la pinza neumática para continuar con la carga y el corte de materiales;
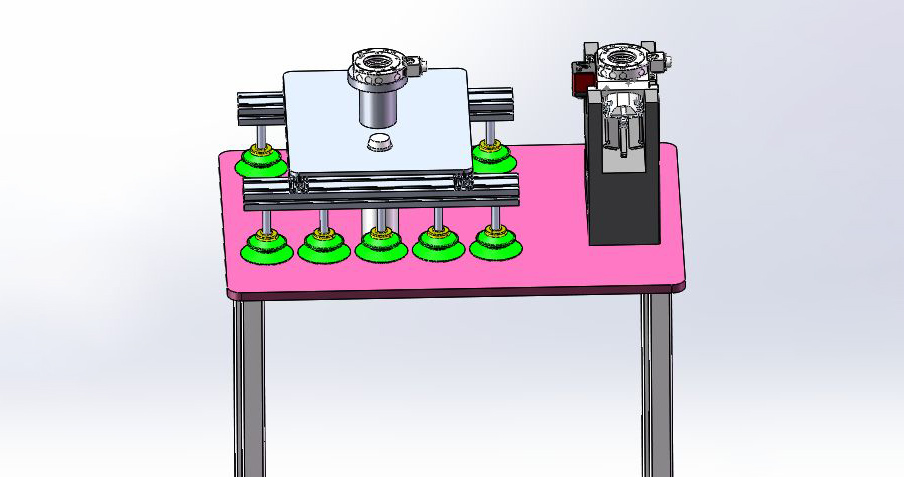
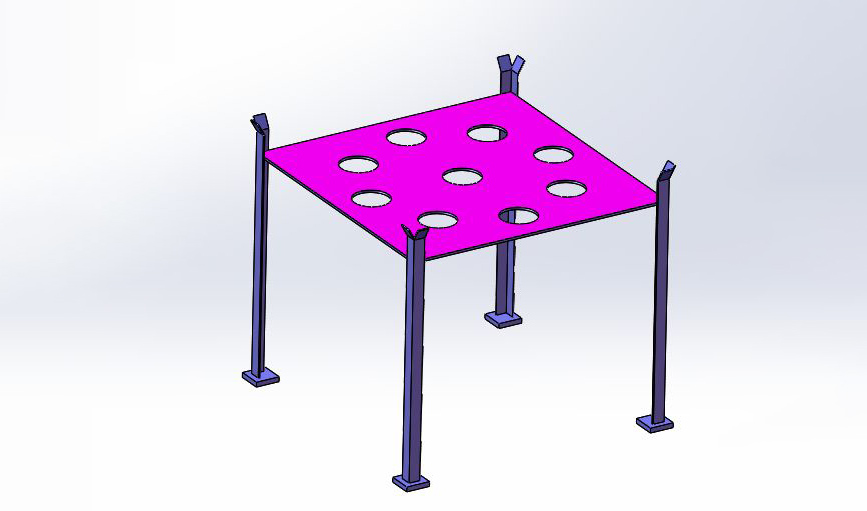
Cesta para almacenamiento temporal de placas divisorias
Introducción a la función
1. Se diseña y planifica una canasta temporal para placas divisorias, ya que las placas divisorias para la carga se retiran primero y las placas divisorias para el corte se utilizan después;
2. Las placas divisorias de carga se colocan manualmente y presentan una consistencia deficiente. Tras colocar la placa divisoria en la cesta de almacenamiento temporal, el robot puede extraerla y colocarla ordenadamente.
Mesa de muestreo manual
Descripción:
1. Establecer diferentes frecuencias de muestreo aleatorio manual para diferentes etapas de producción, lo que puede supervisar eficazmente la efectividad de la medición en línea;
2. Instrucciones de uso: El manipulador colocará la pieza de trabajo en la posición establecida en la mesa de muestreo, según la frecuencia configurada manualmente, y la luz roja lo indicará. El inspector presionará el botón para transportar la pieza de trabajo a la zona de seguridad, fuera de la protección, la extraerá para la medición y la guardará por separado después de la misma.
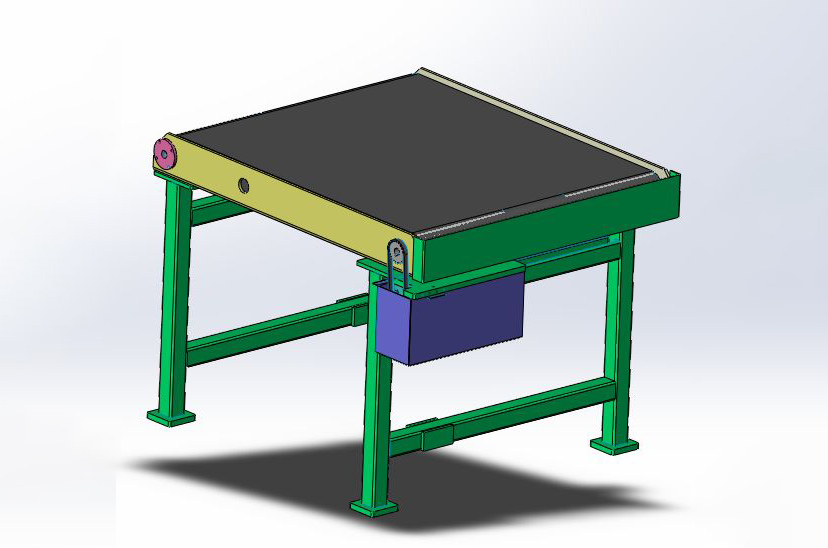
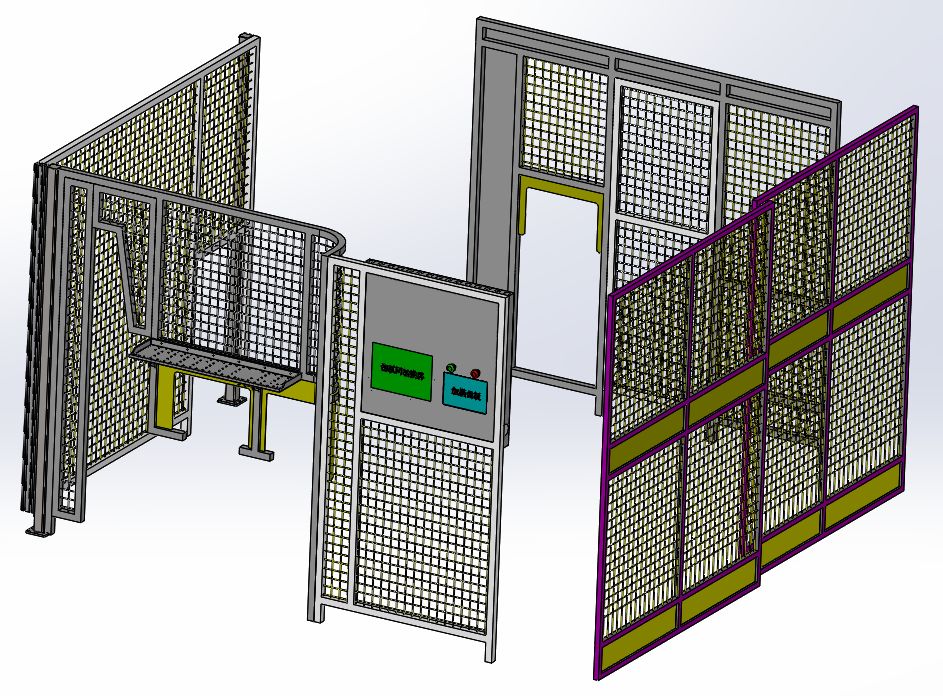
Componentes de protección
Está compuesto por perfil de aluminio ligero (40×40) + malla (50×50), y la pantalla táctil y el botón de parada de emergencia se pueden integrar en los componentes de protección, integrando seguridad y estética.
Introducción del accesorio hidráulico OP20
Instrucciones de procesamiento:
1. Tome el orificio interior φ165 como orificio base, tome el dato D como plano base y tome el arco exterior del saliente de los dos orificios de montaje como límite angular;
2. Controle la acción de aflojamiento y presión de la placa de presión mediante el comando de la máquina herramienta M para completar el procesamiento de biselado del plano superior del saliente del orificio de montaje, el orificio de montaje 8-φ17 y ambos extremos del orificio;
3. El accesorio tiene las funciones de posicionamiento, sujeción automática, detección de hermeticidad, aflojamiento automático, expulsión automática, lavado automático de viruta y limpieza automática del plano de referencia de posicionamiento;
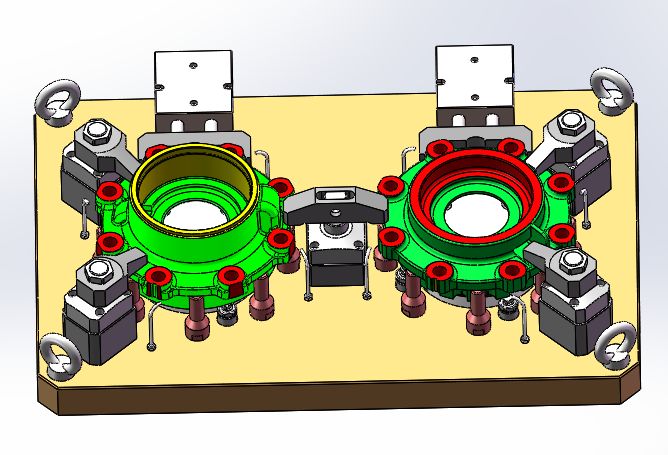
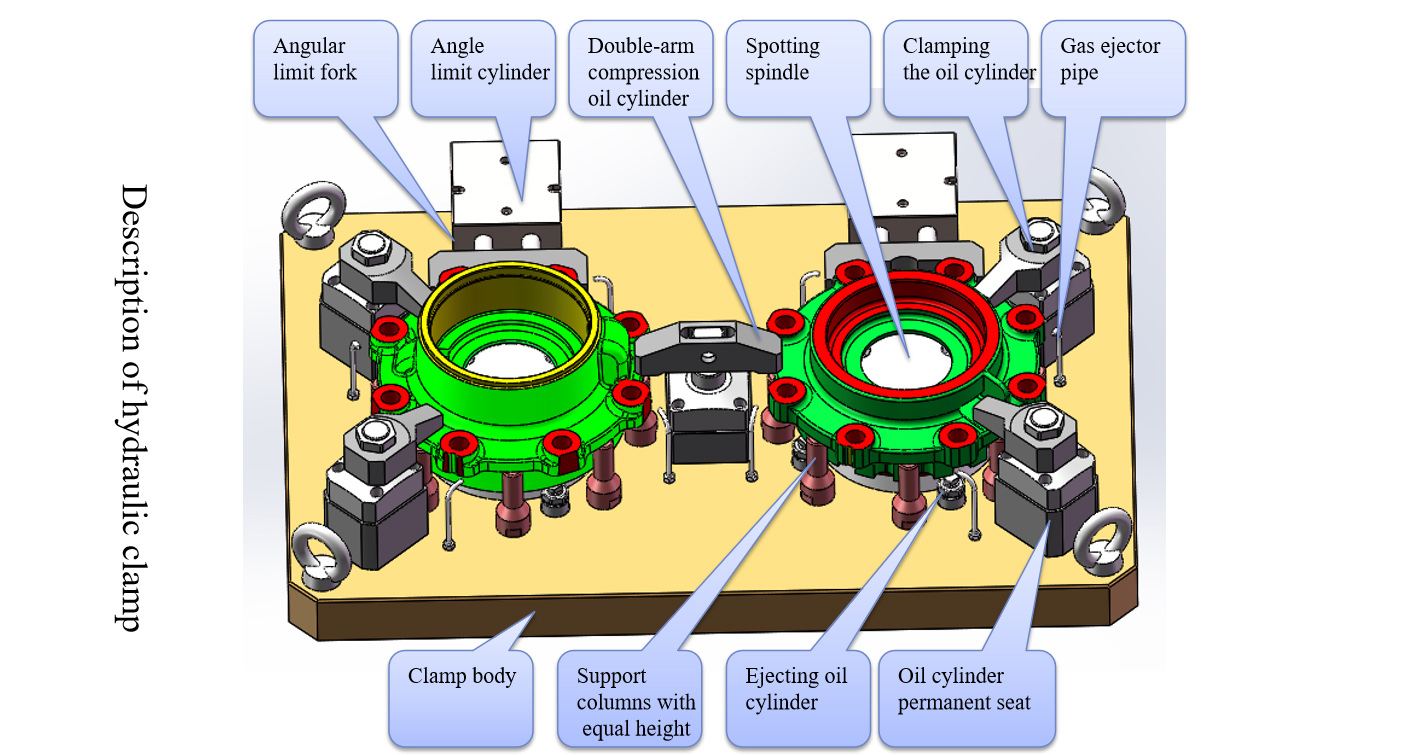
Requisitos de equipo para la línea de producción
1. La abrazadera del equipo de la línea de producción tiene las funciones de sujeción y aflojamiento automáticos y realiza funciones de sujeción y aflojamiento automáticos bajo el control de las señales del sistema manipulador para cooperar con la acción de carga y corte;
2. La posición del tragaluz o módulo de puerta automática se reservará para la placa metálica del equipo de la línea de producción, para coordinar con la señal de control eléctrico y la comunicación del manipulador de nuestra empresa;
3. El equipo de la línea de producción tiene comunicación con el manipulador a través del modo de conexión del conector de carga pesada (o enchufe de aviación);
4. El equipo de la línea de producción tiene un espacio interno (de interferencia) más grande que el rango seguro de acción de la mandíbula del manipulador;
5. El equipo de la línea de producción debe garantizar la ausencia de virutas de hierro residuales en la superficie de posicionamiento de la abrazadera. Si es necesario, se aumentará el soplado de aire para la limpieza (el mandril debe girar durante la limpieza).
6. El equipo de la línea de producción cuenta con un buen sistema de rotura de virutas. De ser necesario, se instalará el dispositivo auxiliar de rotura de virutas de alta presión de nuestra empresa.
7. Cuando el equipo de la línea de producción requiera una parada precisa del husillo de la máquina herramienta, agregue esta función y proporcione las señales eléctricas correspondientes;
Introducción del torno vertical VTC-W9035
El torno vertical NC VTC-W9035 es ideal para el mecanizado de piezas rotativas como piezas brutas de engranajes, bridas y carcasas con formas especiales. Es especialmente adecuado para el torneado preciso, eficiente y de bajo coste de piezas como discos, cubos, discos de freno, cuerpos de bombas, cuerpos de válvulas y carcasas. Esta máquina herramienta ofrece las ventajas de una buena rigidez general, alta precisión, alta tasa de arranque de metal por unidad de tiempo, buena retención de la precisión, alta fiabilidad, fácil mantenimiento, etc., y una amplia gama de aplicaciones. Producción en línea, alta eficiencia y bajo coste.
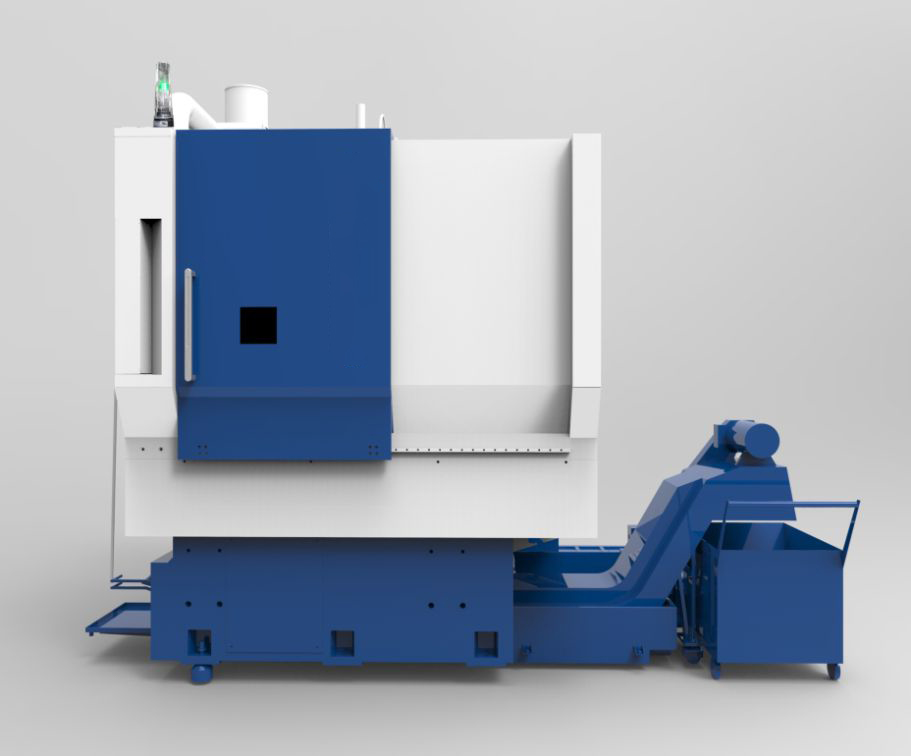
Tipo de modelo | VTC-W9035 |
Diámetro máximo de giro del cuerpo de la cama | Φ900 mm |
Diámetro máximo de giro en placa deslizante | Φ590 mm |
Diámetro máximo de torneado de la pieza de trabajo | Φ850 mm |
Longitud máxima de torneado de la pieza de trabajo | 700 milímetros |
Rango de velocidad del husillo | 20-900 rpm |
Sistema | FANUC 0i-TF |
Recorrido máximo del eje X/Z | 600/800 milímetros |
Velocidad de movimiento rápida del eje X/Z | 20/20 m/min |
Longitud, anchura y altura de la máquina herramienta | 3550*2200*3950 milímetros |
Proyectos | Unidad | Parámetro | |
Rango de procesamiento | Recorrido del eje X | mm | 1100 |
Recorrido del eje X | mm | 610 | |
Recorrido del eje X | mm | 610 | |
Distancia desde la punta del husillo hasta el banco de trabajo | mm | 150~760 | |
Banco de trabajo | Tamaño del banco de trabajo | mm | 1200×600 |
Carga máxima del banco de trabajo | kg | 1000 | |
Ranura en T (tamaño × cantidad × espaciado) | mm | 18×5×100 | |
Alimentación | Velocidad de alimentación rápida del eje X/Y/Z | m/min | 36/36/24 |
Huso | Modo de conducción | Tipo de cinturón | |
Cono del husillo | BT40 | ||
Velocidad máxima de funcionamiento | r/min | 8000 | |
Potencia (nominal/máxima) | KW | 11/18.5 | |
Par (nominal/máximo) | Nuevo Méjico | 52.5/118 | |
Exactitud | Precisión de posicionamiento del eje X/Y/Z (bucle semicerrado) | mm | 0,008 (longitud total) |
Precisión de repetición de los ejes X/Y/Z (bucle semicerrado) | mm | 0,005 (longitud total) | |
Almacén de herramientas | Tipo | Desct | |
Capacidad del almacén de herramientas | 24 | ||
Tamaño máximo de la herramienta(Diámetro de herramienta completo/diámetro de herramienta adyacente vacía/longitud) | mm | Φ78/Φ150/ 300 | |
Peso máximo de la herramienta | kg | 8 | |
Misceláneas | Presión de suministro de aire | MPa | 0.65 |
Capacidad de potencia | KVA | 25 | |
Dimensiones generales de la máquina herramienta (largo × ancho × alto) | mm | 2900×2800×3200 | |
Peso de la máquina herramienta | kg | 7000 |
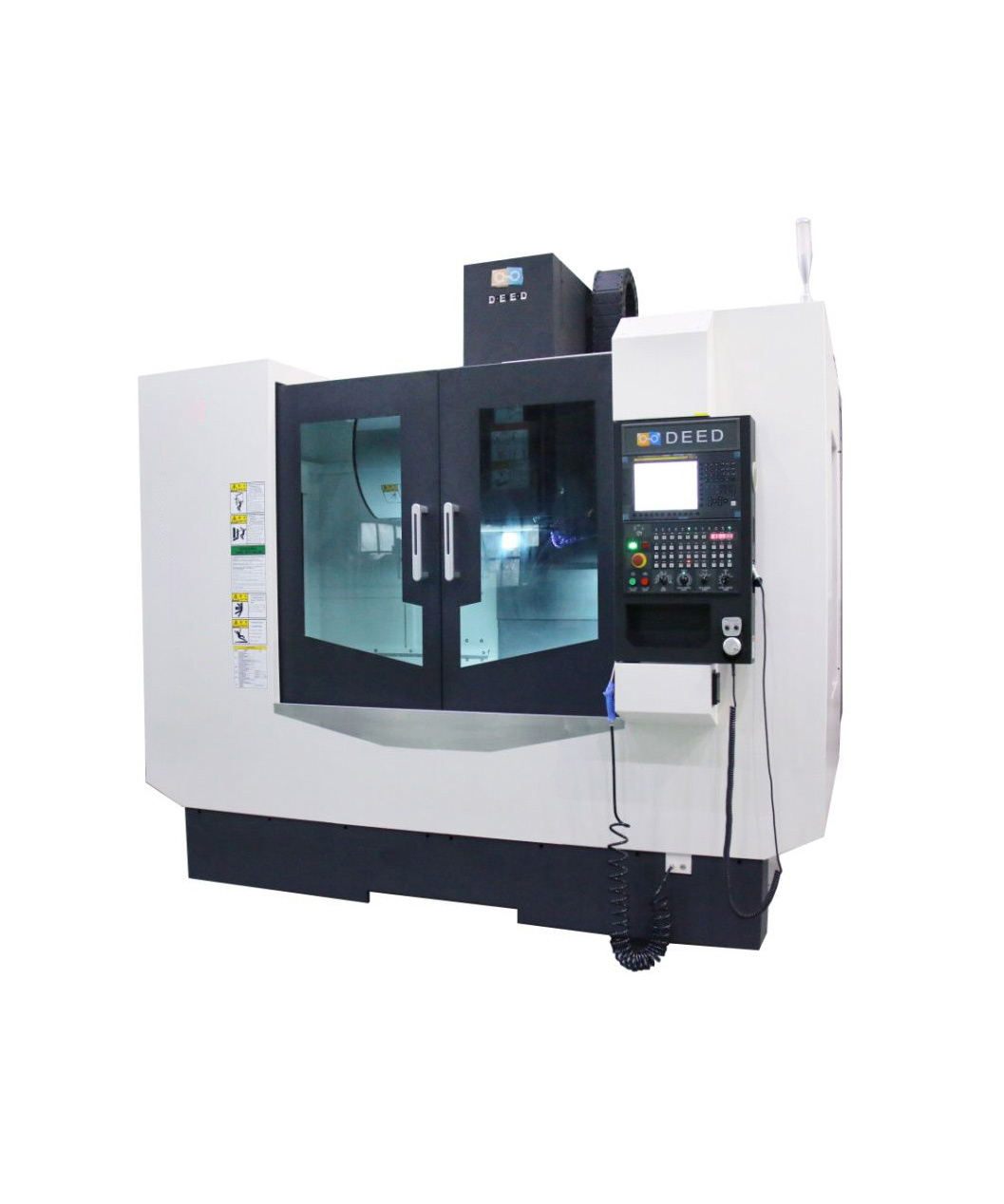